ADDRESS DURING THE INAUGURATION OF 58TH ANNUAL SESSION OF INDIAN INSTITUTE OF CHEMICAL ENGINEERS CHEMCON-2005
14-12-2005 : Delhi
Energy Efficiency Leads to Economic Growth
I am delighted to participate in the inauguration of 58th Annual Session of Indian Institute of Chemical Engineers (CHEMCON-2005) organized by the Indian Institute of Chemical Engineers. I greet the organizers, chemical engineers, scientists, academicians, industrialists and other participants on this occasion. I am glad that the theme of CHEMCON 2005 is "Sustainable Technologies for Efficient Energy Utilization in Process Industries" which is most timely and essential in the current energy scenario of the nation. Sustainable Energy Solutions comes out of Energy Independence. I would like to discuss on the topic "Energy Efficiency Leads to Economic Growth".
As you are aware, our industries and service sectors account for nearly 60% of total energy used in the country and the current national energy shortage is around 7 to 9%. Hence, major innovations are needed for reducing the energy intensity in manufacturing process and reduce the overall energy consumption and emission of pollutants in process industry while increasing the overall efficiency of the process. Such action will save the energy usage by the industry and improve its productivity and profitability, facilitate the electricity boards to meet the demands of the citizens without undue shortage and also help in minimizing the atmospheric pollution.
Now I would like to dwell on the topic of how economic prosperity for the industry and nation can be achieved through the application of innovative energy efficiency measures in India?s chemical process industry.
Strategies for Energy Efficiency
The potential for improvement in energy efficiency in industrial processes depends on how closely such processes have approached their thermodynamic limit. In industrial processes which require moderate temperature and pressures we can introduce technologies for combined heat and power for achieving overall higher efficiency. New process schemes, substitution of material, changes in design and manufacture of products result in less material use and increased recycling can lead to substantial reduction in energy intensity.
Certain technologies that can have strong impact on efficient energy use are microwave processing, electro separation, electro chemical synthesis, ozone disinfection and radio frequency drying. In Pulp and Paper industries the use of membrane separation and bio-filtration can be introduced. In food processing industries ozonation and ultra-violet light for sterilization, electron beam processing and electronic pasteurization for meat and poultry can enable large scale saving in energy and also make the process clean.
In other words,
(a) Improving the efficiency of mechanical, electrical, electronic and chemical plant, equipment, processes and materials,
(b) Reduction in process heat losses and
(c) Use of waste process heat for energy generation
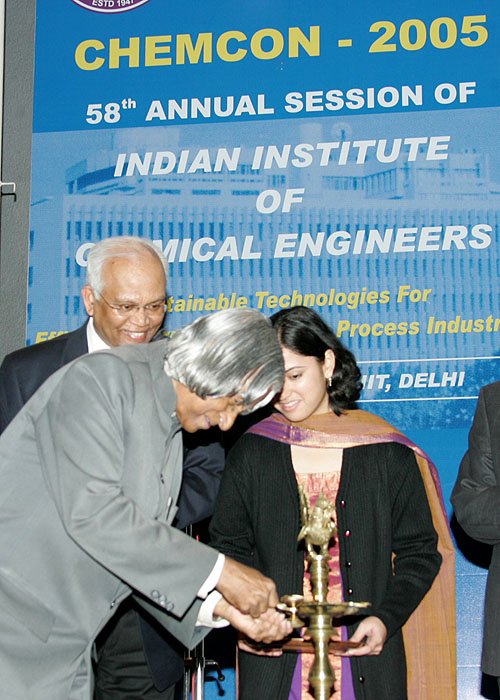
These are the three conventional pillars for enhancing energy efficiency in process industries. In addition, I would like to suggest
(d) A fourth pillar, namely the creative use of renewable energies such as solar and bio-fuel combinations for production of high quality process water for use in boilers and other auxiliary systems and applications thus making them less dependent on depleting resources and increasing costs of oil and natural gas. I understand that a small technology demonstrator "Suryajal" is functional at IIT, Chennai.
I would like to discuss a few case studies to illustrate these points.
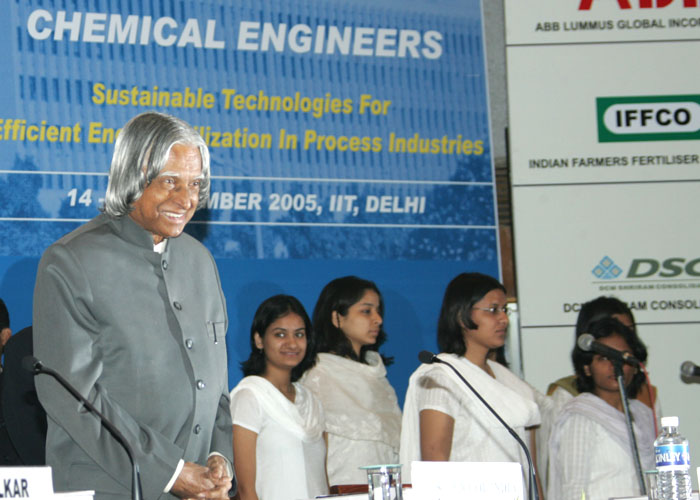

Energy Efficiency in the Sugarcane Industry
As you are all aware, India is the second largest producer of sugar in the world next to Brazil. There are 553 sugar mills operational in the country producing 20 million tonnes per annum of sugar from 360 million tonnes of sugarcane, cultivated by 45 million farmers. I shall now discuss how enhancement of energy efficiency will benefit these major stakeholders in the sugar industry, farming community and the nation.
The yield of crystalline sugar from unit mass of sugarcane is an important parameter for maintaining the competitiveness of the sugar farmers and industry. In the agricultural component of the sugar industry, development of varieties of sugarcane to maximize the yield of crystalline sugar content in a particular variety takes a large amount of time. The typical research potential in sugarcane development is the following:
(a) reduction of water required for cultivation (b) reduction of growth cycle (c) minimizing the cost of input for sugarcane cultivation and also sugar production (d) regulated growth cycle of sugarcane so that sugarcane industries can get continuous supply of sugarcane.
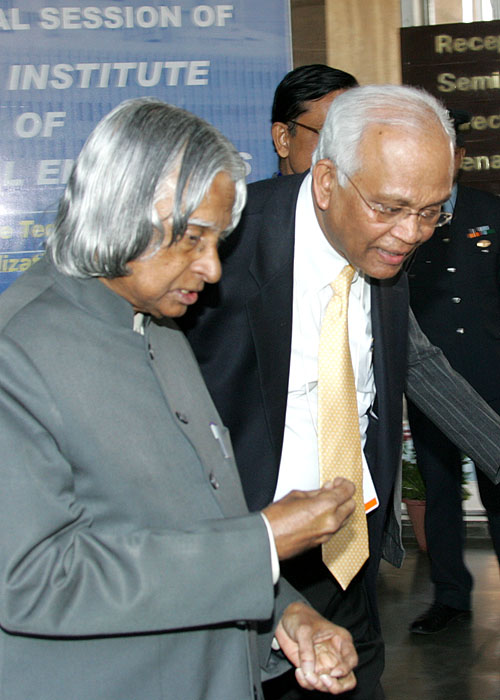
Our scientists have been able to evolve newer sugarcane varieties through micro-propagation so that new transgenic varieties can be grown in States like Maharashtra. Genetic engineering research has to be intensified on molecular characterization of the sugarcane genome, molecular diagnosis of diseases and molecular biology of sugarcane pathogens and nitrogen fixing micro-organisms. The molecular characterization of sugarcane genome will be useful in early selection of desirable plants in the breeding programme on the basis of molecular markets. It is also envisaged to isolate desirable genes (for resistance to biotic and abiotic stresses) from the wild relative species of sugarcane so as to transfer them in the cultivated varieties. Molecular characterization of the disease causing organisms like viruses is useful in controlling the diseases. Development of higher nitrogen fixing microbes will be useful in sustainable and low cost sugarcane production.
So far, I have discussed how the basic bio-technology can lead to high crystalline sugar yielding sugarcane. With this high yielding sugarcane the overall energy requirement for extraction of sugar, per tonne of sugarcane can come down dramatically.
In the sugar industry itself, the Sugar Technology Mission of TIFAC-DST has identified and commercially evaluated equipment and systems to reduce the existing captive power consumption from 35 kilowatts per tonne of sugarcane to 25 kilowatts per tonne that is enhancing the energy efficiency by about 28%. This is being done by improving mechanical efficiency of pumps, compressors, crushers, electric motors, conveyors, continuous centrifuges, continuous vacuum pans etc. New process innovation such as using new Low Pressure Extraction process, flash recovery, recirculation of condensates etc. have also contributed to overall energy savings. In addition, saving in energy has also been accomplished through enhancing the efficiency of electrical and electronic equipment such as variable frequency drive, selective process automation, automation of condensing and cooling systems etc.
The average production of a sugar plant in India is about 35,000 tonnes per annum, with a sugarcane input of above 6.3 lakh tonnes for the plant. By implementing such energy efficiency measures the industry can save about 63 million units of energy. This would result in financial saving of Rs. 32 crore for an average plant or about Rs.18,000 crore per annum for the industry as a whole. This has direct bearing on the profitability of the industry.
I would recommend such measures must be followed by every member of the Indian sugar industry.

Impact of Process Yield Enhancement in the Bio-fuel Industry
Let me now take another example. The rise in oil prices and the dwindling reserve of oil and natural gas makes the transportation sector of our national economy highly vulnerable. However, we have nearly 63 million hectares of wasteland available in the country, out of which 33 million hectares of wasteland have been allotted for tree plantation. One of the bio-fuel generating plant varieties Jatropha can grow well in this wasteland with limited water and fertilizer inputs. The plant has fifty years of life. Fruiting can take place in this plant in two years. It yields up to five tonnes of oil seeds per hectares and presently produces around 1.5 tonnes of bio-fuel. The challenge before our scientists and engineers is to enhance the yield of bio-fuel from the present 1.5 tonnes to 2.5 tonnes per 5 tonnes of oil seeds. Enhancing energy efficiency in the chemical, mechanical, electrical and electronics engineering processes involved in bio-fuel production would contribute to such an enhancement in the yield of bio-fuel plants. In India we are currently importing the large size esterification plants. Our engineers and R&D scientists and the industry should focus in designing, building the energy efficient chemical reactors for small, medium and large esterification plants for use by different segments of Jatropha producers.
This contribution that is enhancing the yield of bio-fuel from Jatropha seeds and building energy efficient chemical reactors for esterification by our scientists and chemical engineers will enhance the nation?s production capacity of bio-fuel by 33 million tonnes. This would be a substantial contribution to India?s oil economy in the era of dwindling supplies and consequent high cost of oil. As you are aware, Government has authorized use of 10% bio-fuel with diesel for small transport sectors. However, the experiments established that 100% bio-fuel use for tractors, trucks, heavy vehicles and diesel generators is technically feasible. A big movement has started for cultivation of Jatropha in millions of hectares in states like Chattisgarh, Andhra Pradesh, Jharkhand and our railways.

Energy Efficiency in Fertilizer Industry
Let me illustrate this with one example. Indian Farmers and Fertilizers Co-operative Organization (IFFCO), is a Cooperative owned by more than 37000 cooperative societies (50 Million farmers) and is the largest producer of fertilizers in the country. It produces over 60 lakh tonnes of fertilizers annually.
IFFCO, in their Phulpur-I plant situated in Allahabad have adopted the following strategies for operating its plants in an energy efficient way. This Plant started its commercial production from March 1981 with overall Specific Energy Consumption of 10.40 Million Kilo calories per Metric Tonne of Urea.
With continuous efforts, the operating efficiency has been increased. Increasing the efficiency of mechanical equipment was carried out by updating of plant and machinery, by replacing earlier technology devices such as turbines, pumps etc. Improving the efficiency of electrical and electronic systems was carried out by installation of a distributed control system by using which the plant was operated closer to optimal design operating parameters. Process heat losses were cut down by micro-level reengineering such as use of better thermal protection insulation of pipelines and vessels, plant effluents have been recycled and used for horticultural and process purposes, thus saving on the overall requirement for process water.
Through the combined action on all these areas the specific energy consumption has been reduced to 7.62 Million Kilo calorie per Metric Tonne Urea by the year 2004-05, amounting to more than 25% reduction in Energy Consumption. This reduction in Energy consumption has saved around 1.5 lakh MT Naphtha per year costing more than Rs. 375 crore per year based on present Energy costs.
The Unit has undertaken more reforms to further lower the Energy consumption to achieve 7.22 Million Kcal/MT urea by May 2006 and is considering the use of renewable energy sources for further reducing dependency on thermal power from fossil fuel sources.
In the area of better material utilization, the Unit shall be switching over from high cost Feedstock Fuel namely Naphtha Fuel Oil to low cost Re-gasified Liquid Natural gas (RLNG). This shall make the Plant further Energy efficient and also reduce the Government subsidy outgo by Rs. 270 crore. The total reduction in subsidy outgo due to above measures shall amount Rs. 645 crore per year. In addition, IFFCO is installing a Carbon Di-Oxide Recovery (CDR) Plant of 450 MTPD capacity to recover CO2 from flue gases, emission of Green House Gases (GHG) to atmosphere thus protecting the environment. The Carbon thus saved shall be traded under Kyoto Protocol to generate additional revenues.

Conclusion
In conclusion, I suggest that the members of the Indian Institute of Chemical Engineers may like to study and standardize and propagate such models among all the fertilizers, sugar and other chemical process industries within the country. This will enable the enhancement of the competitiveness of India's chemical process industries in the international arena.
I have described four basic strategies for enhancing the energy efficiency of chemical plants in a sustainable and profitable manner, through case studies of success stories in sugar and fertilizer industries. These basic strategies can be similarly applied to the entire spectrum of chemical process industries, such as pharmaceuticals and drugs, petroleum refineries, etc. Indeed these principles can be applied by other major engineering industries with significant advantages, such as steel, cement and thermal power industries among a few. Collectively they consume 50% of the total energy consumption in India which is about 1000 billion units. An energy saving target of even a modest 20% in the industrial sector will be a saving of 100 billion units which is worth about Rs. 50,000 crores annually. Look after the small things, and the big things will soon take care of themselves.
I inaugurate CHEMCON 2005 and my best wishes to the participants in their mission of generating sustainable technologies for efficient energy utilization in process industry and lead India towards energy independence.
May God bless you.
<<Back
|